Automated Robotic Manufacturing Cell
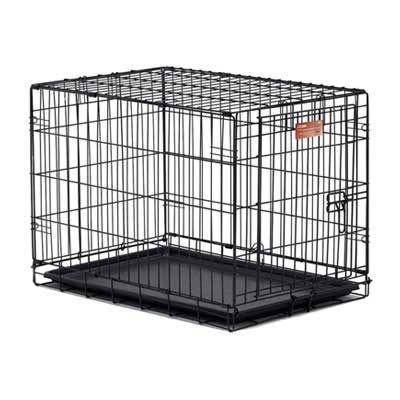
HIGHLIGHTS OF THIS WIRE PET HOME FABRICATION CELL PROJECT
Pet Home
Primary: Development – CAD Drawing
Wire Fabrication:
- Straight and Cut
- Schlatter (wire mesh)
- Trimming
- Press-Brake Forming
- Welding: Resistance Press Welding
Secondary:
Assembly
Powder Coating
Schlatter
Air Toggle Presses
Wire Straight and Cut, Lewis and RMG’s
Break Press, Hurco, CNC
Robotic Pick and Place, Motoman
Length: 40″
Width: 30″
Height: 36″
±.039″ (±1.0mm)
±2ᵒ
9ga and 1/4″ 1008 PQ (plating quality) Wire
Powder Coated, Zinc Plated
Fixture and Jigs, go and no-go fixtures and supervisor inspection. First Article Quality testing with the CMM (Coordinate Measurement Machine).
Adherence and Impact Resistance Testing
Pet Industry, Pet Homes, Pet Cages
100,000 units
1 month
Distribution Centers all across the US
Customer Specifications, 2D CAD Drawings
Pet Home
Was manufactured in an automated robotic cell with pick and place robots to produce the panels for a Pet Home.We developed custom made machinery with the machinery manufacturer with roughly $2.3 million in new machinery and automation.
- 16 Robots, Vision Inspection Systems (to ensure specific complicated parts were going through correctly), Automated Orientation, Part Feeding Systems, Specialty Built Resistance Welding Equipment, and a complete software interface system for full automation.
The company who did the technology integration said the door frame cell was, “the most difficult robotic cell they have built.”